Construction Time & Cost Calculations: Techniques & Formulas
Overview of Time & Cost Calculations in Construction
In the construction industry, time and cost calculations are critical elements that determine the success of a project. These calculations help in planning, budgeting, and scheduling construction activities. Accurate estimations ensure that projects are completed on time and within the allocated budget, avoiding delays and unexpected costs.
Time calculations involve estimating the duration required to complete different phases of a project, while cost calculations involve determining the total expenditure, including labor, materials, and overheads. Both aspects are interdependent, as delays in time can often lead to increased costs, and vice versa.
Importance of Accurate Calculations for Project Success
Accurate time and cost calculations are essential for the overall success of any construction project. Here's why:
- Budget Management: Proper cost estimation helps in creating a realistic budget, reducing the chances of overspending and financial issues during the project.
- Efficient Resource Allocation: Accurate time and cost forecasts allow for better planning and resource allocation, ensuring that labor and materials are available when needed.
- Client Satisfaction: Completing a project on time and within budget helps maintain a positive relationship with clients, increasing trust and the likelihood of future contracts.
- Risk Reduction: Understanding the time and cost factors in advance helps identify potential risks and challenges, enabling contractors to take preventive measures.
- Improved Decision-Making: Accurate calculations provide stakeholders with the necessary data to make informed decisions, optimizing the overall project execution.
Inaccurate calculations can result in delays, cost overruns, or even project failure. Therefore, mastering time and cost calculation techniques is crucial for every construction professional.
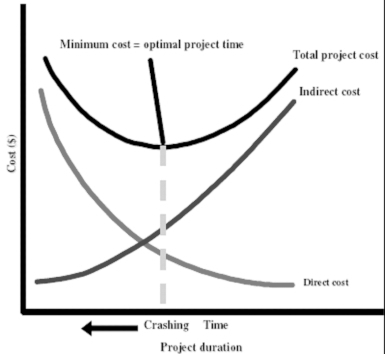
Understanding Construction Time Estimation
Construction time estimation is the process of predicting the time required to complete a construction project or specific phases of the project. Accurate time estimates are essential for creating realistic project schedules, avoiding delays, and ensuring that all tasks are completed within the allocated time frame.
Factors Affecting Construction Time
Several factors can influence the time required to complete a construction project. These factors include:
- Project Scope: A larger or more complex project will naturally require more time for completion.
- Weather Conditions: Adverse weather can cause delays, especially in outdoor construction projects.
- Availability of Labor: The size and skill level of the workforce will impact how efficiently tasks are completed.
- Material Availability: Delays in the supply of materials can cause significant disruptions to the construction timeline.
- Regulatory Approvals and Permits: Delays in obtaining necessary permits or meeting regulatory requirements can extend the project duration.
- Equipment Availability: The availability of specialized machinery or equipment can influence the speed at which construction progresses.
- Project Management and Coordination: Effective management and coordination of all stakeholders can minimize inefficiencies and reduce delays.
Techniques for Estimating Construction Time
Several techniques can be used to estimate construction time effectively. Some of the most common methods include:
- Expert Judgment: Experienced professionals can provide estimates based on their knowledge of similar projects and typical construction timelines.
- Historical Data: Using data from previous projects of a similar nature helps to create a more accurate time estimate.
- Work Breakdown Structure (WBS): This technique divides the project into smaller, more manageable tasks, each with its own time estimate. These estimates are then aggregated to determine the overall project time.
- Critical Path Method (CPM): CPM is a detailed approach where the critical tasks are identified, and the overall time for the project is determined by analyzing the longest sequence of dependent tasks.
- Program Evaluation and Review Technique (PERT): PERT is a statistical tool used to analyze the time required to complete tasks and to assess the probability of completing a project within a certain time frame. It is often used for projects with uncertain durations.
Key Formulas for Time Calculation
Here are some key formulas used in construction time calculations:
- Critical Path Method (CPM) Formula:
The total duration of the project is determined by the sum of the longest path of dependent tasks. This path is known as the critical path.
Project Duration = Sum of Critical Path Task Durations
- Average Duration Formula:
The average time to complete a task can be calculated by using the formula:
Average Duration = (Optimistic Duration + 4 × Most Likely Duration + Pessimistic Duration) / 6
- Work Breakdown Structure (WBS) Formula:
The overall project time is the sum of individual task durations:
Project Duration = Sum of Task Durations (from WBS)
These formulas help in planning and scheduling construction projects, ensuring that the estimated time aligns with the project's scope and resources.
Construction Cost Estimation Basics
Construction cost estimation is the process of predicting the total cost required to complete a construction project. It involves assessing various costs, such as labor, materials, equipment, and overhead, to create an accurate budget. Accurate cost estimation is essential to ensure that a project stays within budget, avoiding unexpected expenses and delays.
Types of Costs in Construction Projects
In construction projects, costs can be categorized into different types. The main types of costs include:
- Direct Costs: These are costs directly associated with the construction process, such as labor, materials, and equipment used for the project.
- Indirect Costs: Also known as overhead, these costs are not directly linked to the construction process but are necessary for project completion. Examples include project management, insurance, and utilities.
- Fixed Costs: Fixed costs remain constant throughout the project. These costs do not change regardless of the project's progress. Examples include administrative expenses and permanent equipment costs.
- Variable Costs: Variable costs change depending on the project's scope or progress. Examples include labor costs, material costs, and fuel expenses.
- Contingency Costs: These are extra costs included in the budget to account for unforeseen circumstances or risks. They help mitigate the impact of unexpected changes or issues during construction.
The Importance of Accurate Cost Estimation
Accurate cost estimation plays a critical role in the success of a construction project. The key reasons for its importance include:
- Budget Control: Accurate cost estimates ensure that the project stays within the allocated budget, preventing cost overruns that could result in financial difficulties or project delays.
- Resource Planning: Knowing the estimated costs helps allocate resources more efficiently, ensuring that the necessary materials, labor, and equipment are available when required.
- Risk Management: Identifying potential cost risks and including contingency funds in the budget helps mitigate financial issues that may arise during construction.
- Client Satisfaction: Providing accurate cost estimates to clients allows for better planning and trust-building. Clients will appreciate transparency and a realistic understanding of the project's financial requirements.
- Decision-Making: Accurate cost estimations provide stakeholders with the necessary information to make informed decisions about project scope, budgeting, and timelines.
Methods for Estimating Costs
There are several methods used to estimate construction costs. The choice of method depends on the project's size, complexity, and available information. Some of the common methods include:
- Analogous Estimating (Top-Down Estimating): This method uses data from previous similar projects to estimate costs. It is often used in the early stages when limited information is available.
- Parametric Estimating: This technique involves using mathematical models or formulas based on project parameters (e.g., cost per square foot or unit) to estimate the overall cost.
- Bottom-Up Estimating: This detailed method involves estimating the cost of each individual task or component of the project and then summing these estimates to determine the total cost.
- Expert Judgment: Experienced professionals can provide cost estimates based on their knowledge of similar projects, industry standards, and local conditions.
- Quantity Takeoff Estimating: This method involves measuring the quantity of materials needed for the project and calculating their costs based on current market prices.
Each of these methods has its advantages and drawbacks, and often a combination of techniques is used to produce the most accurate estimate possible.
Techniques for Time and Cost Optimization
Time and cost optimization is crucial in construction projects to ensure efficiency and minimize unnecessary expenses. By using effective project scheduling tools, implementing cost-control strategies, and applying time-saving techniques, construction professionals can deliver projects on time and within budget.
Project Scheduling Tools
Project scheduling tools help plan, organize, and track the progress of construction projects. These tools enable teams to allocate resources efficiently, monitor task dependencies, and identify potential delays. Some common scheduling tools include:
- Gantt Charts: Gantt charts are visual tools that display the project's timeline, breaking down tasks and showing their start and end dates. They help in tracking progress and identifying delays.
- Critical Path Method (CPM) Software: CPM software helps identify the critical tasks that determine the project's overall duration. By focusing on these tasks, project managers can optimize time and prevent delays.
- Project Management Software: Tools like Microsoft Project, Procore, and Buildertrend offer comprehensive scheduling and project tracking capabilities, allowing teams to manage timelines, budgets, and resources more effectively.
- Work Breakdown Structure (WBS): WBS helps break the project down into smaller, manageable tasks, each with a clear timeline. This detailed approach makes it easier to monitor the project's overall progress and make adjustments as needed.
Cost-Control Strategies
Implementing effective cost-control strategies ensures that construction projects remain within budget. Key cost-control strategies include:
- Detailed Budgeting: Creating a detailed and realistic budget that accounts for all expected costs, including direct, indirect, fixed, and variable costs, helps prevent overspending.
- Regular Cost Monitoring: Continuously monitoring expenses during construction allows for early identification of any budget deviations. Project managers can then take corrective action to prevent further cost overruns.
- Negotiating with Suppliers: Establishing strong relationships with suppliers and negotiating better prices or bulk discounts can help reduce material costs.
- Contingency Planning: Including contingency funds in the budget provides flexibility to address unforeseen issues or changes in the project scope without jeopardizing the overall budget.
- Value Engineering: This technique involves evaluating alternative materials, designs, and methods that provide the same performance at a lower cost, helping to reduce overall project expenses.
Time-Saving Techniques in Construction
Optimizing time in construction projects is essential for meeting deadlines and increasing project efficiency. Here are several time-saving techniques that can be implemented:
- Pre-fabrication: Using pre-fabricated components for construction, such as pre-cast concrete or modular units, can significantly reduce construction time and labor costs.
- Lean Construction: Lean construction focuses on eliminating waste, optimizing workflows, and improving the efficiency of each construction activity. It emphasizes continuous improvement and value delivery.
- Effective Project Communication: Clear communication between all project stakeholders (contractors, clients, suppliers) helps prevent misunderstandings and delays, ensuring smoother progress.
- Task Prioritization: Identifying and prioritizing critical tasks ensures that the most important work is completed first, preventing bottlenecks and maintaining a steady workflow throughout the project.
- Technology Integration: Incorporating advanced technologies such as Building Information Modeling (BIM) allows for better planning, visualization, and collaboration, reducing rework and delays.
- Worker Training and Efficiency: Training workers to perform their tasks efficiently and safely can reduce delays caused by errors or accidents, ensuring the project stays on track.
By integrating these time-saving techniques, project managers can minimize delays, improve productivity, and ensure projects are completed on time, benefiting both the client and the construction team.
Common Formulas for Time & Cost Calculations
In construction projects, using the right formulas for time and cost calculations is essential for accurate estimates and efficient project management. These formulas help in predicting project timelines and budget requirements, leading to better planning and decision-making.
Time-Related Formulas
Time-related formulas help calculate the duration of tasks and the overall project. Here are some key time-related formulas:
- Critical Path Method (CPM) Formula:
The critical path method is used to determine the longest sequence of tasks that must be completed on time to ensure the project finishes on schedule. The formula to calculate the project's duration is:
Project Duration = Sum of Critical Path Task Durations
- Average Duration Formula:
This formula calculates the average time required for a task using three estimates: optimistic (O), most likely (M), and pessimistic (P). The formula is:
Average Duration = (O + 4M + P) / 6
- Lag Time Formula:
Lag time refers to the delay between the end of one task and the start of another. The formula to calculate lag time is:
Lag Time = Successor Task Start Time - Predecessor Task End Time
Cost-Related Formulas
Cost-related formulas are used to estimate the total cost of a project and its individual tasks. Here are some common cost-related formulas:
- Direct Cost Formula:
Direct costs refer to the expenses directly tied to a specific task or project phase. The formula to calculate direct costs is:
Direct Cost = Labor Costs + Material Costs + Equipment Costs
- Indirect Cost Formula:
Indirect costs are overhead costs not directly linked to specific tasks. The formula to calculate indirect costs is:
Indirect Cost = Total Overhead Expenses / Total Project Duration
- Contingency Cost Formula:
Contingency costs are set aside for unforeseen circumstances. The formula to calculate contingency costs is:
Contingency Cost = Total Estimated Cost × Contingency Percentage
- Cost per Unit Formula:
This formula is used to calculate the cost per unit of materials or labor:
Cost per Unit = Total Cost / Number of Units
- Earned Value Management (EVM) Formula:
EVM is used to track project performance and progress. The formula to calculate Earned Value (EV) is:
EV = % of Completed Work × Budget at Completion
Examples of Application
Here are some examples of how these formulas can be applied in construction projects:
- Example 1: Critical Path Method (CPM)
A project has five tasks: A (2 days), B (5 days), C (3 days), D (4 days), and E (1 day). If the tasks depend on each other, the critical path is the longest path, and the total project duration is calculated by summing the critical tasks' durations. If tasks A, B, and D form the critical path, the total project duration is 2 + 5 + 4 = 11 days.
- Example 2: Average Duration Formula
A task has an optimistic duration of 2 days, a most likely duration of 5 days, and a pessimistic duration of 8 days. The average duration is calculated as:
Average Duration = (2 + 4×5 + 8) / 6 = 5 days
- Example 3: Direct Cost Calculation
A construction project has the following costs: $10,000 for labor, $15,000 for materials, and $5,000 for equipment. The direct cost of the project is:
Direct Cost = $10,000 + $15,000 + $5,000 = $30,000
- Example 4: Earned Value Management (EVM)
If 50% of the work is completed and the total budget for the project is $100,000, the Earned Value (EV) is:
EV = 50% × $100,000 = $50,000
These formulas are essential tools for managing time and costs effectively throughout the project lifecycle. By applying them correctly, construction professionals can ensure better planning, monitoring, and control of construction projects.
Using Software and Tools for Time & Cost Calculations
In today’s construction industry, using specialized software and tools for time and cost calculations is essential for streamlining project management processes. These tools help in creating accurate estimates, tracking project progress, and ensuring that construction projects are completed on time and within budget.
Popular Construction Estimation Software
Several construction estimation software programs are widely used in the industry to calculate time and costs. These tools offer various features to help professionals in accurate project planning and management. Some popular options include:
- Procore: Procore is a comprehensive construction management platform that offers tools for project budgeting, scheduling, and time tracking. It allows users to create detailed cost estimates and track time spent on tasks in real time.
- Buildertrend: Buildertrend is a cloud-based software that helps in estimating costs, scheduling projects, and managing budgets. It provides tools for real-time collaboration between contractors, clients, and project teams.
- Microsoft Project: Microsoft Project is a widely used project management software that offers powerful scheduling and budgeting tools. It is commonly used for creating Gantt charts, tracking project timelines, and estimating costs based on resource allocation.
- Construction Cost Estimator (by Clear Estimates): This software provides accurate cost estimation for residential construction projects. It allows users to generate detailed cost breakdowns based on current material and labor rates.
- CoConstruct: CoConstruct is a construction management platform that helps with cost estimating, project budgeting, and time scheduling. It includes tools for creating client-friendly estimates and tracking project expenses.
- PlanSwift: PlanSwift is a takeoff and estimating software that allows users to measure digital plans and calculate material quantities. It helps speed up the estimating process by providing accurate material and labor cost calculations.
Benefits of Digital Tools in Construction Calculations
Digital tools and software have become essential for improving accuracy, saving time, and enhancing project management in construction. The main benefits of using digital tools for time and cost calculations include:
- Improved Accuracy: Software tools help minimize human errors in calculations, ensuring that time and cost estimates are more accurate. This helps in creating reliable budgets and schedules that are less likely to experience unforeseen overruns.
- Time Efficiency: Digital tools automate many aspects of time and cost calculations, speeding up the estimation process. Tasks such as measuring quantities, calculating material costs, and creating schedules are all streamlined, saving significant time.
- Real-Time Tracking: Many construction management software programs offer real-time tracking features. Project managers can monitor costs and timelines as the project progresses, allowing for quick adjustments if necessary.
- Better Collaboration: Digital tools enable better collaboration among all stakeholders in a construction project. With cloud-based platforms, teams can access and update project data from anywhere, ensuring that everyone stays on the same page.
- Customizable Reports: Construction estimation software allows users to generate customizable reports that highlight key project metrics, such as total costs, labor expenses, and project timelines. This is particularly useful for tracking the financial health and progress of a project.
- Integration with Other Tools: Many software platforms integrate with other construction tools, such as accounting software or building information modeling (BIM) tools. This allows for seamless data sharing and reduces the need for manual input across different platforms.
- Cost Control: Digital tools help project managers control costs more effectively by providing visibility into ongoing expenses. They can track labor, material, and overhead costs and compare them with the original budget, helping to identify potential cost overruns early on.
- Scalability: Many construction estimation software tools are scalable, meaning they can be used for both small and large projects. As the complexity of a project increases, digital tools can adapt to handle larger datasets and more detailed calculations.
By using digital tools for time and cost calculations, construction professionals can optimize project management, reduce risks, and improve the efficiency of their operations, ultimately leading to the successful completion of projects.
Case Studies and Practical Examples
Case studies and practical examples provide valuable insights into how time and cost calculations are applied in real-world construction projects. By analyzing these examples, construction professionals can improve the accuracy of their own estimates and make better decisions throughout the project lifecycle.
Real-Life Examples of Time & Cost Calculations
Here are a few real-life examples of how time and cost calculations were applied in construction projects:
- Example 1: Residential Building Project
A residential construction project estimated the total construction time using the Critical Path Method (CPM). After identifying the critical path, the total project duration was calculated to be 12 months. However, due to unexpected weather delays, the project took an additional 2 months to complete, resulting in a 15% cost overrun due to extended labor costs and material storage. This case highlights the importance of factoring in potential delays when estimating time and costs.
- Example 2: Commercial Office Complex
In a commercial office construction project, cost estimation was performed using historical data and quantity takeoffs. The original budget was $5 million, but unexpected material price increases caused a 10% increase in overall costs. However, the project team had included contingency costs, which helped to absorb this increase without causing major disruptions. This case demonstrates the value of including contingency funds in cost estimation to manage unforeseen costs.
- Example 3: Infrastructure Project
An infrastructure project involving the construction of a new highway used software tools to integrate scheduling and budgeting. The project had a total cost estimate of $100 million, but by using detailed time and cost calculations, the team was able to optimize resources, reduce waste, and finish the project 3 months ahead of schedule, while staying within budget. This example illustrates how advanced software tools can lead to better optimization and more efficient project management.
Analyzing Case Studies for Improved Accuracy
By analyzing case studies, construction professionals can identify key factors that contribute to the accuracy of time and cost estimates. Below are some lessons learned from case studies:
- Lesson 1: Importance of Accurate Data
In most case studies, the accuracy of historical data and the use of reliable cost estimation methods were crucial for accurate time and cost calculations. Using outdated or inaccurate data can lead to significant discrepancies between estimates and actual costs.
- Lesson 2: Factor in Contingencies
Many case studies show that projects that included contingency budgets were better able to absorb unforeseen costs, such as material price hikes or unexpected delays. This emphasizes the need for flexibility in cost estimation and the importance of planning for the unexpected.
- Lesson 3: Real-Time Monitoring and Adjustments
Projects that utilized real-time tracking of costs and schedules were able to make timely adjustments, minimizing the impact of any deviations. This shows the value of having software tools that allow project managers to monitor progress and adjust resources or timelines as needed.
- Lesson 4: Collaboration Between Stakeholders
Case studies highlight that successful projects often involved clear and continuous communication between contractors, clients, and suppliers. When all stakeholders are on the same page, it is easier to make accurate time and cost estimates and adjust them as the project progresses.
- Lesson 5: Flexibility in Time Estimates
Many case studies reveal that while time estimates are critical, they must also be flexible. Delays due to factors such as weather, labor shortages, or unforeseen site conditions are common, and projects that planned for these delays had more accurate completion dates.
By analyzing these case studies and practical examples, construction professionals can refine their estimation processes, improve accuracy, and enhance the overall efficiency of their projects. These lessons can help avoid common pitfalls and lead to better decision-making in both time and cost calculations.
Common Mistakes in Time & Cost Calculations
Time and cost calculations are essential for the smooth execution of construction projects. However, mistakes in estimation can lead to delays, cost overruns, and project failures. Identifying common errors and understanding how to avoid them can significantly improve the accuracy of your estimates and contribute to the success of a project.
Identifying Errors in Estimation
Errors in time and cost estimation can occur due to a variety of factors. Recognizing these errors early can help mitigate their impact. Some common errors include:
- Underestimating Task Durations: One of the most common mistakes is underestimating the time required to complete tasks. This can happen when previous experiences are applied without considering the specific challenges of the current project.
- Ignoring Contingencies: Failing to include contingency costs or time buffers can lead to problems when unforeseen issues arise, such as bad weather, supply delays, or labor shortages.
- Overlooking Dependencies: Not accounting for task dependencies can lead to inaccurate schedules. For example, a task that relies on the completion of another task cannot start until the first task is finished, which may lead to delays if not properly considered.
- Not Accounting for Resource Constraints: Not properly considering the availability of labor, equipment, or materials can result in unrealistic time estimates and cost projections. This is particularly true for large projects with many moving parts.
- Using Outdated or Inaccurate Data: Relying on outdated or inaccurate cost data can lead to significant errors in estimating labor and material costs. Always use the most current data available to ensure accuracy.
- Underestimating Complexity: Complex projects often require more time and resources than initially expected. Failing to account for this complexity in the estimation process can lead to delays and cost overruns.
How to Avoid Common Calculation Mistakes
To avoid common calculation mistakes, it is essential to adopt best practices and use appropriate methods for estimating time and costs. Here are some strategies to improve the accuracy of your calculations:
- Use Detailed Work Breakdown Structures (WBS): Break down the project into smaller, manageable tasks. This will help to better estimate the time and costs for each specific task and ensure that no critical components are overlooked.
- Incorporate Realistic Time Buffers: Always include contingency time in the schedule to account for potential delays. Building in realistic time buffers allows for flexibility when unexpected issues arise.
- Use Historical Data: Refer to data from similar past projects to estimate time and costs. Historical data provides valuable insights into how long tasks took and how much they cost, helping to refine your estimates for the current project.
- Utilize Software Tools: Construction estimation software can help reduce human error by automating calculations, tracking project progress in real time, and offering more accurate time and cost predictions based on data. Software can also help identify errors before they become significant issues.
- Consult Experts and Collaborate: When estimating complex projects, consult with experienced professionals who have worked on similar projects. Collaboration with all stakeholders—such as contractors, suppliers, and project managers—helps to ensure that all aspects of the project are considered when making estimations.
- Account for Task Dependencies: Always account for dependencies between tasks. Using tools like Gantt charts or Critical Path Method (CPM) can help visualize task dependencies and avoid scheduling errors.
- Monitor and Update Estimates Regularly: As the project progresses, continually monitor the actual time and costs against the estimates. Adjust the estimates as necessary based on new information, changing circumstances, or any issues that arise. This helps keep the project on track and ensures better future planning.
- Review and Revise Estimates: Before finalizing the project budget and schedule, review and revise your estimates multiple times to ensure accuracy. It can be helpful to get feedback from other team members to identify potential mistakes and gaps in the initial calculations.
By applying these strategies and avoiding common estimation errors, construction professionals can improve the accuracy of their time and cost calculations. This leads to better project planning, improved resource allocation, and, ultimately, more successful project outcomes.
Conclusion
Accurate time and cost calculations are fundamental to the successful completion of any construction project. Proper estimation ensures that projects stay within budget, are completed on time, and meet the expectations of clients and stakeholders. By understanding the key techniques, formulas, and tools available for time and cost estimation, construction professionals can improve their planning and decision-making processes.
It's essential to consider all relevant factors, such as task dependencies, resource availability, and potential risks, when estimating time and costs. Furthermore, integrating modern software tools can significantly enhance accuracy and efficiency, allowing for real-time tracking and adjustments. Analyzing case studies and learning from past mistakes can also provide valuable insights into refining the estimation process and avoiding common errors.
Ultimately, the ability to make accurate time and cost estimates will not only help keep projects on track but also foster better relationships with clients, reduce risks, and contribute to the overall success and reputation of the construction team. By continuously refining estimation practices and adopting a proactive approach, construction professionals can deliver projects that meet deadlines, stay within budget, and achieve the desired results.
FAQs
Here are some frequently asked questions related to time and cost calculations in construction projects:
1. Why is accurate time estimation important in construction?
Accurate time estimation helps ensure that construction projects are completed on schedule. It allows project managers to allocate resources effectively, avoid unnecessary delays, and set realistic expectations for clients. Accurate time estimation also helps to minimize disruptions and avoid the negative impact of prolonged project durations on costs.
2. What are the main types of costs involved in construction projects?
The main types of costs in construction projects include direct costs (such as labor, materials, and equipment), indirect costs (overhead expenses like insurance, utilities, and project management), and contingency costs (funds set aside for unexpected expenses). Properly estimating and managing these costs is key to staying within budget.
3. How can I avoid cost overruns in my construction project?
To avoid cost overruns, it is crucial to create a detailed and realistic budget, monitor expenses regularly, include contingency funds for unforeseen costs, and use accurate cost estimation methods. Additionally, maintaining clear communication with all stakeholders and negotiating with suppliers can help manage and control costs more effectively.
4. What is the Critical Path Method (CPM), and how is it used in time estimation?
The Critical Path Method (CPM) is a project management tool used to identify the longest sequence of dependent tasks, known as the "critical path." This path determines the minimum project duration. CPM helps project managers focus on critical tasks to ensure that delays in these areas do not affect the overall project timeline.
5. How do I estimate costs for a construction project?
Cost estimation can be done using several methods, including historical data from similar projects, quantity takeoff estimating (calculating material quantities), and expert judgment. It’s also helpful to use construction estimation software for accurate and detailed cost predictions. A good practice is to account for all possible costs, including labor, materials, equipment, and overheads, as well as include contingency funds for unexpected costs.
6. How do software tools help with time and cost calculations?
Software tools help streamline time and cost calculations by automating many tasks, providing real-time data tracking, and offering accurate predictions based on historical data and project parameters. Tools like Microsoft Project, Procore, and Buildertrend help construction professionals create detailed schedules, track progress, manage resources, and monitor costs effectively, leading to improved project efficiency and reduced errors.
7. What should I do if my project is falling behind schedule?
If your project is falling behind schedule, it's important to identify the root cause of the delays and make necessary adjustments. You can optimize the schedule by reallocating resources, speeding up tasks on the critical path, and adjusting timelines where possible. Open communication with stakeholders and a review of project dependencies can help find solutions and get the project back on track.
8. How can I ensure accurate cost estimates for materials?
To ensure accurate cost estimates for materials, you should use up-to-date pricing data, consider bulk discounts or negotiated prices with suppliers, and take into account potential price fluctuations. Using quantity takeoff software or estimators can help ensure that the amount of materials needed is calculated precisely, reducing the chance of overordering or running out of supplies.
References
- Project Management for Construction – Chris Hendrickson – 2008 – Carnegie Mellon University
- Construction Project Management: A Practical Guide – Alison Dykstra – 2011 – Kirshner Publishing
- Fundamentals of Construction Estimating – David Pratt – 2011 – Cengage Learning
- Construction Management JumpStart – Barbara J. Jackson – 2010 – Wiley
- Estimating in Building Construction – Steven J. Peterson, Frank R. Dagostino – 2013 – Pearson
- Construction Planning and Scheduling – Jimmie Hinze – 2011 – Pearson Education
- Modern Construction Management – Frank Harris, Ronald McCaffer, Francis Edum-Fotwe – 2013 – Wiley-Blackwell
- Construction Cost Estimating for Project Control – Peurifoy and Oberlender – 2002 – McGraw-Hill
- Managing the Construction Process – Frederick E. Gould – 2004 – Pearson Prentice Hall
- Construction Project Scheduling and Control – Saleh Mubarak – 2010 – Wiley