Construction Cost Calculations: A Comprehensive Step-by-Step Guide
What Is Construction Cost Calculation?
Construction cost calculation is the process of estimating the total expenses required to complete a construction project. It includes various cost components such as materials, labor, equipment, permits, and unexpected contingencies. A well-structured cost calculation helps ensure that the project stays within budget and avoids financial overruns.
Why Is Accurate Cost Estimation Important?
Accurate cost estimation is crucial for the success of any construction project. It helps in:
- Budget Planning: Ensures that the project is financially feasible before starting.
- Resource Allocation: Helps in efficient distribution of materials, labor, and equipment.
- Risk Management: Minimizes unexpected expenses by accounting for potential cost fluctuations.
- Project Scheduling: Ensures timely completion by aligning resources and finances.
- Client Confidence: Builds trust with stakeholders by providing realistic cost projections.
By using precise calculations, construction managers can avoid delays, disputes, and financial losses, leading to a smoother project execution.
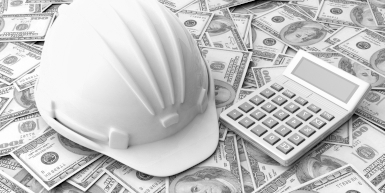
Understanding Construction Costs
Before starting a construction project, it's essential to understand the different types of costs involved. These costs can be categorized based on their nature and impact on the overall budget.
Direct vs. Indirect Costs
Direct costs are expenses that are directly tied to the construction project. These include:
- Materials (cement, steel, bricks, etc.)
- Labor wages
- Equipment and machinery rentals
Indirect costs are expenses that support the project but are not directly linked to construction activities. These include:
- Project management and supervision
- Administrative expenses
- Insurance and permits
Fixed vs. Variable Costs
Fixed costs remain constant regardless of project size or duration. Examples include:
- Land purchase costs
- Architectural and engineering fees
- Construction site setup expenses
Variable costs change depending on the scope of work, material prices, and labor hours. Examples include:
- Hourly wages for workers
- Material costs based on market fluctuations
- Equipment rental charges based on usage
One-Time vs. Recurring Costs
One-time costs occur only once during the project and do not repeat. These include:
- Land acquisition
- Initial site preparation
- Major equipment purchases
Recurring costs are expenses that continue throughout the project or even after its completion. These include:
- Monthly labor wages
- Maintenance and repairs
- Utility bills during construction
Understanding these cost categories helps in creating a more accurate budget and avoiding financial surprises during the project.
Step 1: Defining Project Scope
Defining the project scope is the first and most crucial step in construction cost calculations. A well-defined scope ensures clarity, prevents cost overruns, and helps in efficient planning.
Identifying Project Requirements
To create an accurate cost estimate, it is essential to identify the project's key requirements, including:
- Project Type: Residential, commercial, industrial, or infrastructure.
- Size and Complexity: Number of floors, rooms, or specialized features.
- Design and Specifications: Architectural plans, materials, and finishes.
- Location and Site Conditions: Land conditions, accessibility, and environmental factors.
- Regulatory Requirements: Permits, zoning laws, and compliance standards.
By gathering this information early, construction planners can make informed decisions about materials, labor, and overall costs.
Setting a Budget Framework
Once the project requirements are established, setting a realistic budget is the next step. The budget should include:
- Estimated Construction Costs: Materials, labor, equipment, and subcontractor fees.
- Permits and Legal Fees: Local government approvals and licenses.
- Contingency Fund: A buffer (typically 10-20% of total cost) for unexpected expenses.
- Financing Considerations: Loans, grants, or other funding sources.
A well-planned budget helps keep the project on track and ensures financial stability throughout construction.
Step 2: Estimating Material Costs
Material costs form a significant portion of the total construction budget. Accurate estimation ensures that the right materials are procured within budget, preventing shortages or overspending.
Common Construction Materials and Their Costs
Construction materials vary based on project type, location, and quality requirements. Some of the most commonly used materials include:
- Cement: Essential for concrete structures, foundations, and masonry work.
- Bricks and Blocks: Used for walls, partitions, and structural support.
- Steel and Reinforcement Bars: Critical for structural stability in beams, columns, and slabs.
- Sand and Gravel: Key components in concrete and plastering work.
- Wood: Used for framing, flooring, doors, and windows.
- Glass: Commonly used for windows, facades, and interior partitions.
- Electrical and Plumbing Materials: Includes wiring, pipes, fittings, and insulation.
- Paints and Finishes: Essential for aesthetics, weather protection, and durability.
The cost of these materials depends on market rates, quality, and transportation expenses.
How to Source Cost-Effective Materials
To reduce material costs without compromising quality, consider the following strategies:
- Bulk Purchasing: Buying materials in large quantities often results in discounts.
- Compare Suppliers: Research multiple suppliers to find the best price and quality balance.
- Use Local Materials: Reduces transportation costs and ensures quicker availability.
- Consider Alternative Materials: Explore sustainable or cost-effective alternatives that meet project requirements.
- Negotiate Contracts: Secure better pricing by negotiating long-term contracts with reliable suppliers.
- Minimize Waste: Plan precise material requirements to avoid excess and wastage.
Proper planning and strategic sourcing can lead to significant savings while maintaining construction quality.
Step 3: Labor Cost Estimation
Labor costs are a major part of any construction budget, and accurate estimation ensures that the project remains financially viable while maintaining quality and efficiency.
Types of Labor Costs
Labor costs in construction are generally classified into three main categories:
- Skilled Labor: Includes professionals like electricians, plumbers, carpenters, and masons who require specialized training and certifications.
- Unskilled Labor: Includes general workers who assist with site preparation, material handling, and other basic tasks.
- Subcontractor Labor: Includes specialized workers hired through third-party contractors, such as HVAC technicians and roofing specialists.
Each type of labor has different wage rates, which vary based on experience, location, and industry standards.
Factors That Influence Labor Expenses
Several factors can impact the total labor costs in a construction project:
- Project Size and Complexity: Larger and more intricate projects require more workers and higher skill levels, increasing labor costs.
- Location and Market Rates: Labor costs vary significantly based on the local job market and cost of living.
- Union vs. Non-Union Workers: Hiring unionized workers may involve higher wages and benefits but can provide better work quality and reliability.
- Project Timeline: Tight deadlines may require overtime work, increasing labor expenses.
- Productivity Levels: Highly experienced workers may cost more per hour but complete tasks faster, reducing overall labor hours.
- Seasonal Demand: Labor costs can rise during peak construction seasons due to high demand for workers.
- Safety and Compliance Costs: Additional costs may arise from training, safety equipment, and meeting legal labor standards.
By carefully estimating labor costs and considering these factors, construction managers can create a more accurate and realistic project budget.
Step 4: Equipment and Machinery Costs
Construction projects require various types of equipment and machinery to complete tasks efficiently. Proper cost estimation ensures that the right equipment is used while keeping expenses under control.
Buying vs. Renting Equipment
One of the key decisions in construction planning is whether to buy or rent equipment. Each option has its advantages and cost considerations:
Buying Equipment
Purchasing construction equipment is a long-term investment and is suitable for projects requiring frequent use of machinery.
- Advantages:
- Cost-effective for long-term projects.
- Available for use at any time without rental delays.
- Can be resold after use, recovering part of the investment.
- Disadvantages:
- High upfront costs.
- Requires maintenance, repairs, and storage.
- May become obsolete over time.
Renting Equipment
Renting is ideal for short-term projects or when specialized equipment is needed temporarily.
- Advantages:
- Lower upfront costs.
- No maintenance or storage responsibilities.
- Access to the latest models with modern technology.
- Disadvantages:
- Higher long-term costs if rented frequently.
- Limited availability during peak seasons.
- Rental fees may increase over time.
Maintenance and Operational Costs
Whether buying or renting, equipment requires proper maintenance and operational planning to ensure efficiency and cost-effectiveness.
- Fuel and Energy Costs: Heavy machinery consumes fuel or electricity, contributing to overall expenses.
- Routine Maintenance: Regular servicing, lubrication, and inspections help prevent breakdowns and extend equipment life.
- Repair Costs: Unexpected failures may require costly repairs, especially for owned equipment.
- Storage and Transportation: Large machinery requires designated storage space and transport between job sites.
- Operator Training: Skilled operators are needed to use the equipment safely and efficiently.
By carefully evaluating equipment needs, construction managers can optimize costs and ensure smooth project execution.
Step 5: Permits, Fees, and Legal Costs
Before starting a construction project, obtaining the necessary permits and complying with legal regulations is essential. Failure to do so can result in fines, delays, or even project shutdowns. Estimating these costs in advance helps in budgeting accurately.
Understanding Building Permits
A building permit is an official approval issued by a local government authority that allows construction work to proceed legally. The cost of permits varies based on project type, location, and scale.
Common Types of Building Permits:
- Construction Permit: Required for new buildings, renovations, and major modifications.
- Electrical Permit: Necessary for electrical system installations and upgrades.
- Plumbing Permit: Needed for plumbing work, including water supply and drainage systems.
- Demolition Permit: Required for tearing down structures before new construction.
- Zoning Permit: Ensures the project aligns with local zoning laws and land use regulations.
- Environmental Permit: Mandatory for projects affecting natural resources, such as wetlands or forests.
The application process for permits usually includes plan submissions, inspections, and approval from local authorities. It's important to account for both permit fees and potential delays during approval.
Other Regulatory Costs to Consider
Beyond building permits, several additional legal and compliance costs may arise, including:
- Inspection Fees: Local authorities may charge for periodic inspections to ensure code compliance.
- Impact Fees: Charged by municipalities to offset infrastructure costs, such as roads and utilities.
- Contractor Licensing Fees: Builders and contractors may need to obtain licenses before working on a project.
- Safety Compliance Costs: Includes expenses for workplace safety training, protective equipment, and hazard mitigation.
- Legal and Consultant Fees: Hiring legal experts or consultants to navigate complex regulations can add to costs.
- Insurance Costs: Construction liability insurance, worker’s compensation, and property insurance are often required.
Proper planning and understanding of these costs ensure a smooth construction process while avoiding legal complications.
Step 6: Contingency and Unexpected Costs
Even with careful planning, unexpected expenses can arise during construction. A contingency budget helps cover these unforeseen costs, ensuring the project stays on track without financial strain.
Why You Need a Contingency Budget
A contingency budget is a reserve fund set aside to handle unexpected expenses that may arise during construction. This helps in:
- Managing Unforeseen Issues: Covers unexpected structural problems, delays, or design modifications.
- Preventing Budget Overruns: Acts as a financial cushion to absorb cost fluctuations in materials or labor.
- Avoiding Project Delays: Ensures that unexpected expenses do not halt construction progress.
- Maintaining Quality: Allows adjustments for better materials or additional safety measures without cutting corners.
- Meeting Regulatory Changes: Covers new legal requirements or compliance costs that may arise.
A well-planned contingency budget provides financial security and flexibility throughout the project.
How to Estimate Extra Costs
Estimating a contingency budget requires analyzing potential risks and determining a reasonable reserve amount. Here’s how:
- Standard Contingency Percentage: Most projects allocate 5% to 20% of the total budget for contingencies, depending on project complexity.
- Risk Assessment: Identify high-risk areas such as foundation work, weather-related delays, or material price fluctuations.
- Review Past Projects: Analyze cost overruns in similar projects to estimate a realistic contingency amount.
- Consult with Experts: Seek advice from contractors, engineers, and financial planners to refine cost estimations.
- Track Expenses in Real-Time: Use cost management tools to monitor spending and adjust contingency funds accordingly.
By preparing for unexpected costs in advance, construction managers can ensure smoother project execution without financial setbacks.
Step 7: Finalizing the Cost Estimate
After estimating all costs, the final step is to review and summarize the total budget. A well-structured cost estimate ensures financial accuracy and prevents overspending.
Summarizing All Expenses
To finalize the cost estimate, all expenses should be categorized and totaled. The key cost components include:
- Material Costs: Total cost of raw materials, including cement, bricks, steel, wood, and finishing materials.
- Labor Costs: Wages for skilled and unskilled workers, contractor fees, and subcontractor expenses.
- Equipment and Machinery Costs: Purchase or rental of construction machinery, fuel, and maintenance expenses.
- Permits and Legal Fees: Costs for building permits, inspection fees, zoning permits, and contractor licensing.
- Contingency Budget: A reserve fund (typically 5-20% of the total budget) for unexpected expenses.
- Overhead and Administrative Costs: Office expenses, project management fees, insurance, and other indirect costs.
Summing up all these costs provides a clear view of the total estimated budget required for the construction project.
Reviewing for Accuracy
Before finalizing the estimate, a thorough review is essential to ensure accuracy and avoid costly mistakes. The review process includes:
- Cross-Checking Estimates: Verify calculations and compare them with similar past projects.
- Consulting Experts: Seek feedback from engineers, contractors, and financial planners.
- Accounting for Inflation: Adjust material and labor costs based on market trends.
- Using Cost Estimation Software: Utilize digital tools to refine calculations and reduce human errors.
- Validating Against Project Scope: Ensure all project requirements are included in the estimate.
A well-reviewed and finalized cost estimate helps in securing financing, managing cash flow, and ensuring smooth project execution.
Cost-Saving Strategies in Construction
Managing costs effectively is essential for completing a construction project within budget without compromising quality. Implementing smart budgeting techniques and negotiating effectively with contractors and suppliers can lead to significant savings.
Smart Budgeting Techniques
Careful planning and financial management help reduce costs while ensuring efficiency in construction. Here are some key budgeting strategies:
- Detailed Cost Planning: Break down the budget into specific categories (materials, labor, equipment, permits) for better cost tracking.
- Bulk Purchasing: Buying materials in large quantities often results in discounts and lower per-unit costs.
- Alternative Materials: Consider using cost-effective substitutes without sacrificing durability or safety.
- Efficient Design: Optimize project blueprints to reduce material waste and simplify construction processes.
- Minimize Rework: Proper planning and high-quality workmanship reduce costly mistakes and project delays.
- Energy-Efficient Solutions: Using sustainable materials and efficient HVAC systems can lead to long-term savings.
- Hire Skilled Labor: Experienced workers complete tasks faster and with fewer errors, reducing overall labor costs.
Negotiation Tips for Contractors and Suppliers
Effective negotiation with suppliers and contractors can help secure better deals and reduce expenses. Here’s how:
- Get Multiple Quotes: Compare offers from different suppliers and contractors to find the best price.
- Long-Term Partnerships: Establish relationships with reliable suppliers to negotiate better rates for future projects.
- Transparent Pricing: Request a detailed breakdown of costs to avoid hidden charges.
- Negotiate Payment Terms: Flexible payment plans or bulk payment discounts can help with cash flow management.
- Consider Seasonal Discounts: Purchasing materials during off-peak seasons may lead to cost reductions.
- Use Value Engineering: Work with contractors to identify alternative construction methods that reduce costs while maintaining quality.
By applying these cost-saving strategies, construction managers can optimize resources and maximize project efficiency.
Tools and Software for Cost Calculation
Using digital tools and software for cost estimation can significantly improve accuracy, efficiency, and financial planning in construction projects. These tools help automate calculations, reduce human errors, and provide real-time budget tracking.
Best Digital Tools for Budgeting
Several software solutions are available to assist with construction cost estimation and budgeting. Some of the most popular tools include:
- ProEst: A cloud-based estimating software that helps contractors generate accurate cost estimates and proposals.
- PlanSwift: A takeoff software that allows users to measure and estimate material costs directly from digital blueprints.
- Buildertrend: A project management tool with budgeting features to track costs, invoices, and financial reports.
- RSMeans Data Online: A cost database that provides updated pricing information for materials, labor, and equipment.
- Stack: A cloud-based estimating tool for contractors, offering prebuilt templates and automated calculations.
- Microsoft Excel with Estimation Templates: A customizable solution for creating cost spreadsheets with formulas and macros.
These tools help construction managers stay on top of expenses and optimize budget allocation throughout the project.
How to Use Cost Estimation Software
To maximize the benefits of cost estimation software, follow these steps:
- Select the Right Software: Choose a tool that fits the project scale, budget, and complexity.
- Input Project Details: Enter key information such as project scope, material quantities, labor costs, and equipment expenses.
- Utilize Built-in Cost Databases: Many tools provide updated material and labor cost data for accurate calculations.
- Generate Detailed Estimates: Use the software to break down costs into categories and create itemized budgets.
- Adjust for Market Fluctuations: Update cost data regularly to account for inflation, supply chain changes, and labor rate adjustments.
- Track and Compare Costs: Monitor actual expenses against initial estimates and adjust the budget accordingly.
- Export and Share Reports: Generate cost reports to share with stakeholders, clients, and project teams.
By leveraging cost estimation software, construction teams can improve financial planning, reduce errors, and enhance project efficiency.
Common Mistakes in Construction Cost Estimation
Accurate cost estimation is crucial for keeping a construction project within budget. However, many projects face financial overruns due to common errors in the estimation process. Identifying and avoiding these mistakes can lead to better financial planning and project success.
Errors to Avoid
Some of the most common mistakes in construction cost estimation include:
- Underestimating Material Costs: Failing to account for price fluctuations or material shortages can lead to budget overruns.
- Ignoring Labor Productivity Rates: Overlooking variations in worker efficiency can result in incorrect labor cost estimates.
- Forgetting Contingency Funds: Not allocating a contingency budget can make it difficult to handle unexpected expenses.
- Incomplete Scope Definition: A poorly defined project scope can lead to change orders and additional costs.
- Not Considering Permits and Regulatory Fees: Overlooking permit costs and legal compliance can delay the project and increase expenses.
- Incorrect Quantity Takeoff: Mistakes in material quantity calculations can lead to shortages or excess waste.
- Failure to Include Equipment Costs: Not budgeting for equipment rental, fuel, or maintenance can result in unexpected financial strain.
- Relying on Outdated Cost Data: Using old pricing information can lead to significant discrepancies in estimates.
- Misjudging Project Timelines: Underestimating the duration of work can increase labor and rental costs.
How to Improve Accuracy
To create a more precise cost estimate, consider the following best practices:
- Use Reliable Cost Databases: Refer to up-to-date material and labor cost data from industry sources.
- Leverage Estimation Software: Digital tools help automate calculations and reduce human errors.
- Consult Experienced Professionals: Get input from engineers, contractors, and financial experts to validate cost estimates.
- Perform Regular Reviews: Continuously update cost estimates based on project progress and market changes.
- Conduct a Risk Assessment: Identify potential risks that could impact costs and prepare contingency plans.
- Improve Communication: Ensure clear communication between project managers, suppliers, and contractors to prevent misunderstandings.
- Track Actual Costs: Monitor real-time expenses and compare them with initial estimates to adjust the budget proactively.
By avoiding common mistakes and following these accuracy-improving strategies, construction teams can create more reliable cost estimates and maintain better financial control over their projects.
Conclusion
Accurate construction cost estimation is essential for the success of any project. By following a step-by-step approach, project managers can plan budgets effectively, avoid financial overruns, and ensure smooth execution.
Key takeaways from this guide include:
- Understanding Construction Costs: Differentiating between direct vs. indirect, fixed vs. variable, and one-time vs. recurring costs.
- Defining the Project Scope: Clearly outlining requirements and setting a structured budget framework.
- Estimating Material and Labor Costs: Using cost-effective strategies to balance quality and expenses.
- Accounting for Equipment and Machinery: Choosing between buying or renting and considering maintenance costs.
- Including Permits and Legal Fees: Ensuring compliance with regulations to avoid unexpected fines.
- Planning for Contingencies: Setting aside a reserve budget to handle unforeseen costs.
- Using Digital Tools: Leveraging software solutions to improve cost accuracy and efficiency.
- Avoiding Common Mistakes: Preventing errors such as underestimation, misjudging timelines, and missing critical cost factors.
By implementing these best practices, construction teams can enhance financial control, reduce risks, and improve overall project success. A well-prepared cost estimate not only keeps the project within budget but also builds trust with clients and stakeholders.
With proper planning, strategic cost management, and the right tools, any construction project can be completed efficiently and profitably.
FAQs
1. Why is cost estimation important in construction?
Cost estimation helps project managers create a realistic budget, allocate resources efficiently, and avoid financial overruns. It ensures that the project remains profitable and on schedule.
2. What are the main factors that influence construction costs?
Key factors include material costs, labor wages, equipment expenses, permits and regulatory fees, site conditions, and unexpected contingencies.
3. How can I reduce construction costs without compromising quality?
Strategies include bulk purchasing of materials, using alternative materials, hiring skilled labor for efficiency, negotiating better deals with suppliers, and leveraging cost estimation software.
4. What percentage of the budget should be allocated for contingencies?
Most projects set aside 5% to 20% of the total budget as a contingency fund to cover unexpected costs such as price fluctuations, design changes, or unforeseen site conditions.
5. Should I buy or rent construction equipment?
If the equipment is needed frequently for long-term use, buying may be cost-effective. However, for short-term projects, renting can help reduce upfront costs and maintenance expenses.
6. What is the best software for construction cost estimation?
Popular options include ProEst, PlanSwift, Buildertrend, RSMeans Data Online, and Microsoft Excel with estimation templates. The choice depends on project complexity and budget.
7. How can I ensure accuracy in my cost estimation?
Using updated cost data, consulting industry professionals, leveraging digital tools, tracking real-time expenses, and conducting periodic reviews can help improve accuracy.
8. What are common mistakes in construction cost estimation?
Common errors include underestimating material and labor costs, forgetting contingency funds, not accounting for permits, relying on outdated data, and misjudging project timelines.
9. How often should I update my cost estimate?
It’s recommended to update the cost estimate at key project milestones, whenever material prices change, or if there are modifications to the project scope.
10. How can I negotiate better rates with suppliers and contractors?
Obtain multiple quotes, establish long-term partnerships, negotiate bulk discounts, ask for transparent pricing breakdowns, and consider seasonal price fluctuations.
By understanding these common questions and best practices, construction professionals can better manage their budgets and ensure project success.
References
- Construction Cost Estimating: Process and Practices – Len Holm – 2021 – Routledge
- Estimating in Building Construction – Steven J. Peterson, Frank R. Dagostino – 2019 – Pearson
- Construction Project Management: A Practical Guide – Alison Dykstra – 2011 – Kirshner Publishing
- Means Building Construction Cost Data – RSMeans – 2023 – Gordian
- Fundamentals of Construction Estimating – David Pratt – 2016 – Cengage Learning
- Project Management for Construction – Chris Hendrickson – 2008 – Carnegie Mellon University
- Construction Planning, Equipment, and Methods – Robert L. Peurifoy, Clifford J. Schexnayder, Aviad Shapira – 2019 – McGraw-Hill Education
- Building Construction: Principles, Materials, and Systems – Madan Mehta, Walter Scarborough, Diane Armpriest – 2013 – Pearson